interchangeabilité (suite)
De même qu’il est impossible de fabriquer une pièce mécanique ayant des cotes rigoureusement imposées (tolérances nulles), de même il est impossible de mesurer les dimensions exactes d’une pièce. Quel que soit l’appareil de mesure utilisé, la mesure est entachée d’une erreur, aussi petite soit-elle, résultant de la précision et de la sensibilité de l’appareil de mesure. Si on appelle c la valeur maximale de cette erreur, et T′ et t′ les tolérances de fabrication des arbres et alésages ainsi contrôlées (par exemple avec un calibre à limites), la relation précédente s’écrit en toute rigueur :
(c est par exemple la tolérance de fabrication d’un tampon à limite : tolérance sur le diamètre). L’interchangeabilité des éléments d’un assemblage de deux pièces exige que la tolérance de fonctionnement Jmax – Jmin de cet assemblage (ou tolérance d’ajustement) soit supérieure à la somme des tolérances réelles de fabrication (T + t), ou mieux à la somme des valeurs mesurées des tolérances de fabrication des pièces et des calibres de contrôle utilisés (T′ + t′ + 2 c).
Il ne faut pas confondre précision avec interchangeabilité. En effet, si le premier terme des relations (1) et (2) est suffisamment grand, une fabrication grossière correspondant à de grandes tolérances T et t pourra cependant être interchangeable. Au contraire, si ce premier terme est très petit, une fabrication très précise ne pourra satisfaire à cette condition et, dans quelques cas particuliers, il faut renoncer à l’interchangeabilité : dans certains mécanismes extrêmement précis, il faut prévoir des ajustages au cours du montage ou des réglages après assemblage des éléments constitutifs, opérations qui nécessitent l’intervention de compagnons hautement qualifiés. On peut s’y soustraire en faisant appel à l’apairage. Cette opération consiste à classer en différents groupes l’ensemble des pièces fabriquées de chaque type, de telle manière que la dimension de la cote considérée (cote critique) croisse du premier au dernier lot : par exemple de 2 μ en 2 μ pour le diamètre des pistons de certains équipements hydrauliques de voitures automobiles. Les groupes de pièces mâles (pistons) d’une part et les groupes de pièces femelles (cylindres) d’autre part sont ensuite numérotés séparément de telle manière que toute pièce mâle prise dans l’un des groupes soit interchangeable lorsqu’elle est montée avec n’importe quelle autre pièce femelle prise dans le groupe correspondant de même numéro.
Tolérance
C’est la différence admissible entre la limite supérieure et la limite inférieure d’une cote donnée dans un même lot de pièces qualifiées d’identiques : on parle de tolérance de fabrication. C’est aussi l’écart admissible entre la limite supérieure et la limite inférieure du jeu ou du serrage d’un type d’assemblage donné : il s’agit alors de tolérance d’ajustement ou de tolérance de fonctionnement. En pratique, il est impossible de réaliser des pièces parfaitement identiques ; la répétition du diamètre d’un alésage ou du diamètre de la portée d’un arbre donné, dans une fabrication continue ou intermittente d’un même atelier ou d’ateliers différents, ne peut se faire qu’en laissant à l’exécutant, pour chaque cote, un certain intervalle dans lequel la valeur réelle devra se trouver. Cet intervalle est appelé tolérance de fabrication. Si la cote d’une pièce mâle fabriquée est plus grande que la limite supérieure fixée, on devra reprendre l’usinage de cette pièce ; si au contraire la cote est plus petite que la valeur inférieure de cet intervalle, on devra rejeter la pièce après contrôle et inversement pour la pièce dite « femelle ». Pour plus de commodité, on assigne à la pièce une dimension nominale et on définit chacune des deux limites par son écart par rapport à cette dimension nominale. La valeur absolue et le signe de l’écart s’obtiennent en retranchant la dimension nominale de la limite envisagée.
Les tolérances des pièces mécaniques font l’objet d’une très importante norme internationale ISO, connue sous le titre Système de tolérances et constituée par un ensemble systématique de valeurs de tolérances et d’écarts normalisés, présenté sous forme d’une série de tableaux à deux entrées. Dans cette norme, les dimensions considérées vont de 3 à 500 mm ; les tolérances normalisées sont réparties en douze classes de qualité ; les plus petites valeurs (1 à 4) correspondent aux fabrications les plus précises possible : cales et calibres ; les plus grandes valeurs (9 à 12) correspondent aux fabrications les moins précises : mécanique agricole ; la qualité courante en mécanique générale de précision est la qualité 7. Chaque classe est elle-même subdivisée en une vingtaine de sous-classes, correspondant chacune à des ajustements différents, c’est-à-dire à des types d’assemblages différents. Ces sous-classes sont différenciées par des lettres A... Z pour les alésages ou pièces femelles et a... z pour les arbres ou pièces mâles.
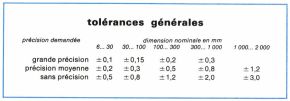
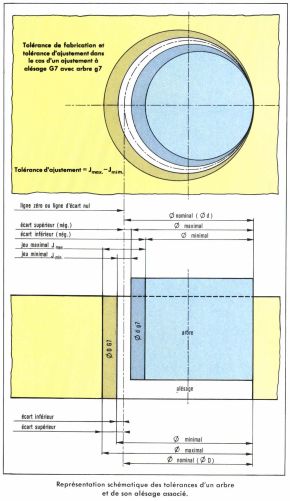
Ajustement
C’est la caractéristique résultant de la différence, avant assemblage, entre les dimensions de deux pièces destinées à être assemblées.
Suivant la position respective des zones de tolérances de l’alésage et de l’arbre (donc suivant la sous-classe A à Z retenue pour l’alésage et la sous-classe a à z retenue pour l’arbre), l’ajustement peut être plus ou moins exact : il peut être soit avec jeu (libre, tournant, glissant, glissant juste), soit avec serrage (légèrement serré, serré, fretté).
Afin de rendre plus rationnel le travail des bureaux d’études ainsi que les opérations d’usinage classiques, un certain nombre d’ajustements sont toujours réalisés à partir des mêmes combinaisons de tolérances, alors qu’il est évident qu’un même résultat peut être obtenu en jouant différemment sur les tolérances d’ajustement d’une pièce ou de l’autre.
En particulier, on cherche toujours à garder les tolérances de la classe 7 pour les pièces femelles et à jouer sur les tolérances des pièces mâles correspondantes pour réaliser l’ajustement recherché.
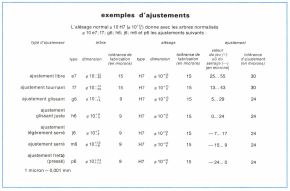
G. F.