sidérurgie (suite)
La fusion de l’acier dans un four à sole fut réussie en 1863 par le Français Pierre Martin (1824-1915) grâce, d’une part, au type de revêtement acide avec briques de silice et de quartz qu’il utilisa et, d’autre part, au système de récupération de chaleur inventé en 1856 par l’Allemand Friedrich von Siemens (1826-1904) avec son frère Wilhelm (1823-1883). Le procédé d’affinage de la fonte au four Martin-Siemens était né, et ce sont les Français Pourcel et Varland qui le perfectionnèrent pour traiter les fontes phosphoreuses avec un revêtement basique.
Après les tentatives à partir de 1885 de l’Italien Ferrari, du Français Henri Moissan (1852-1907) et du Suédois Kjellin pour effectuer la fusion de l’acier au four électrique, la naissance de l’aciérie électrique date de 1900 avec l’invention par le Français Paul Héroult (1863-1914) du four à arc à sole non conductrice.
La période contemporaine
À partir de la Seconde Guerre mondiale, de nouveaux progrès furent réalisés dans les procédés d’élaboration, et de profondes modifications apparurent dans les structures économiques de la sidérurgie. Alors qu’au début du xxe s. le volume intérieur d’un haut fourneau était de l’ordre de 750 m3 avec une production journalière de 500 t de fonte, les récents hauts fourneaux, d’un volume de 4 500 m3, atteignent une production journalière de 10 000 à 13 000 t de fonte. Cette notable augmentation de capacité de production est due aux améliorations propres au haut fourneau (dimensions, profil, soufflage, récupérateur de chaleur Cowper, pression des gaz) et à la nature du minerai, plus riche en fer (minerais importés, enrichis et agglomérés, préréduits). Cette alimentation des appareils en minerais riches a modifié l’implantation des usines sidérurgiques : alors qu’au xixe s. on construisait les usines sidérurgiques près des mines de fer ou près des mines de charbon, les raisons économiques d’approvisionnement en minerais font situer maintenant les complexes sidérurgiques dans des régions portuaires (Dunkerque, Fos-sur-Mer, Le Havre en France ; Gênes, Naples, Tarente en Italie ; etc.), au détriment de régions anciennement industrialisées (Lorraine).
Afin d’obtenir la qualité des aciers Martin avec la capacité de production des convertisseurs Thomas ou Bessemer, de nouveaux procédés d’affinage de la fonte par soufflage à l’oxygène pur ont été introduits à partir de 1949 (procédés LD, Kaldo, O. L. P.), et leur développement est tel qu’aujourd’hui plus de la moitié des aciers se trouve élaborée par ces derniers. De nouvelles mutations provenant de l’application de la coulée continue aux aciers, de la réduction directe des minerais par des gaz hydrocarbonés, de la fusion au four électrique à arc à haute puissance spécifique et des procédés spéciaux de laminage en continu conduisent à des unités de production de semi-produits bien particuliers, les mini-aciéries.
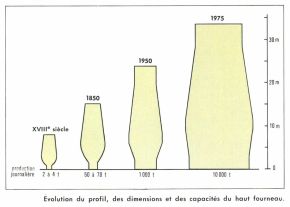

Minerais de fer
Les minerais les plus exploités pour l’élaboration de la fonte au haut fourneau, et titrant de 30 à 70 p. 100 en fer, sont les suivants.
1. Les minerais oxydés anhydres à base d’oxyde ferrique Fe2O3, tels que l’hématite rouge, l’hématite oolithique, l’ocre rouge (composés non cristallisés), sont exploités aux États-Unis (lac Supérieur), en U. R. S. S., en Espagne, en Afrique du Nord, au Brésil, en Angleterre, et le fer ooligiste ou spéculaire, cristallisé, exploité en U. R. S. S. et à l’île d’Elbe.
2. Les minerais oxydés hydratés, ou hématites brunes, ont pour composé de base l’oxyde 2 Fe2O3, 3 H2O, la goéthite ; une variété globulaire ou oolithique constitue la minette phosphoreuse (0,7 p. 100 de phosphore), abondante en Lorraine. Une autre variété oolithique courante, la limonite, se rencontre en U. R. S. S., aux États-Unis et en Suède.
3. Les minerais riches à plus de 60 p. 100 de fer, à base de magnétite Fe3O4, sont extraits en U. R. S. S., en Afrique du Nord et en Suède.
4. Les minerais carbonatés à base de carbonate ferreux FeCO3 sont exploités sous forme soit de sidérose, ou fer spathique (Autriche, Pyrénées Orientales), soit de sphérosidérose, ou fer lithoïde (Allemagne, Grande-Bretagne, Normandie).
5. Les minerais de fer manganésés, recherchés pour l’élaboration de certaines fontes et ferro-alliages, sont extraits en U. R. S. S., au Brésil, en Grèce et en Inde.
Après leur extraction de la mine, les minerais de fer subissent une préparation physique et physico-chimique pour les débarrasser de leur gangue stérile, les amener dans un état physique favorable à leur traitement (porosité, grosseur des particules, tenue mécanique des fragments) et les enrichir. Au lavage, au concassage et au criblage, pratiqués depuis longtemps, ont été adjoints des traitements d’enrichissement soit par grillage pour les minerais carbonatés, soit par grillage et triage magnétique pour les minerais riches en oxyde magnétique Fe3O4, ou bien encore par traitement d’agglomération. Ainsi, le minerai lorrain est aggloméré dans des installations sur tables, fours tournants ou à chaîne continue du type Dwight-Lloyd, ces dernières pouvant atteindre une capacité de production de 15 000 t/j de minerai aggloméré. Un lit d’agglomération — constitué, par exemple, de 78 parties de minerai à 30 p. 100 de fer, 9 parties de minerai à 40 p. 100 de fer, 3 parties de poussières de récupération de gaz de haut fourneau et d’aciérie, 1 partie de battitures de laminage et 9 parties de fines de houille et poussier de coke — permet d’obtenir 65 parties d’aggloméré à 47 p. 100 de fer. Certains procédés d’enrichissement par boulettage ou pelletisation (boulettes ou pellets d’un diamètre de l’ordre de 10 mm) ainsi que la préréduction des minerais contribuent à améliorer le rendement des hauts fourneaux et la qualité de la fonte.
Obtention de la fonte au haut fourneau
Four à cuve de fusion réductrice, le haut fourneau réalise la réduction du minerai de fer par le carbone qui aboutit au fer, mais, en raison du milieu fortement carburant, ce dernier forme un alliage liquide, la fonte, dont la teneur en carbone est de 3 à 4 p. 100 et qui est recueillie à la base de l’appareil. À la partie supérieure de l’installation, dans le gueulard, sont introduites les charges : minerai de fer (brut, aggloméré ou préréduit), coke métallurgique et un fondant, la castine. Le coke métallurgique, caractérisé par sa résistance à l’écrasement, sa porosité et sa pureté (absence de cendres, de soufre, de phosphore), est obtenu par traitement de la houille dans une cokerie, souvent intégrée aux installations sidérurgiques ; son rôle est de servir à la fois de combustible et d’élément réducteur. Le fondant a pour but d’éliminer la gangue du minerai en formant un laitier fusible dont le trou de coulée est situé au-dessus de celui de la fonte. Le fondant doit être adapté à la nature de la gangue. Celle-ci étant généralement siliceuse et alumineuse, le fondant est constitué par de la castine à base de carbonate de calcium, ce qui aboutit à la formation d’un laitier de silico-aluminate de calcium.