traitement thermique (suite)
Le durcissement structural se manifeste avec d’autres alliages que les alliages légers à base d’aluminium. Ce traitement est employé pour certains cupro-alliages (cupronickels au silicium et à l’aluminium, cuprobéryllium avec additions de chrome, de cobalt ou de zirconium), les alliages de magnésium-aluminium et les aciers maraging, contenant 0,03 p. 100 de carbone, 18 p. 100 de nickel, 8 p. 100 de cobalt, 4 p. 100 de molybdène et 0,5 p. 100 de titane.
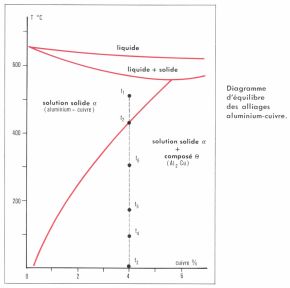
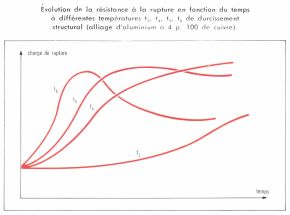
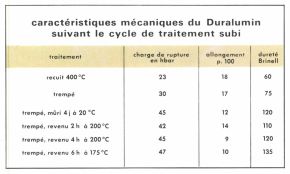
Traitements thermomécaniques
Des traitements particuliers sont maintenant pratiqués par déformation des pièces en acier (forgeage, laminage, étirage, tréfilage) au cours de divers cycles de traitement thermique, généralement dans le domaine de la transformation isotherme de l’austénite instable vers 500 °C (austéniformage) ou vers 700 °C (isoformage), ou encore à plus haute température, supérieure à A3 dans le domaine de l’austénite stable. Après formage, les pièces subissent la suite du traitement thermique par trempe et revenu. Ces traitements présentent l’intérêt d’améliorer les caractéristiques mécaniques des pièces, particulièrement leur résistance à la fatigue et leur tenue aux chocs à basse température. Ils étaient pratiqués déjà de façon limitée par grenaillage des pièces en acier (déformation superficielle) durant leur traitement de trempe isotherme martensitique.
Traitements thermochimiques
Les traitements thermochimiques ou de cémentation sont directement liés aux traitements thermiques proprement dits par les phénomènes structuraux qui les gouvernent (diffusion atomique), par les installations industrielles qui les réalisent et par la nécessité, pour plusieurs d’entre eux, de les accompagner de traitements de trempe et de revenu. Ils ont pour objet de modifier les propriétés superficielles des métaux et des alliages, soit pour augmenter leurs caractéristiques mécaniques (dureté, résistance à la rupture), soit pour améliorer leurs propriétés de surface (frottement, usure), ou bien encore pour les protéger de la corrosion et de diverses attaques chimiques.
Ils sont réalisés par la diffusion à chaud, à l’état solide, d’un élément (métal ou métalloïde) à partir de la surface d’une pièce métallique déjà ébauchée dans sa forme ou totalement usinée. On traite ainsi les aciers par diffusion de carbone (cémentation proprement dite), d’azote (nitruration), de carbone et d’azote (carbonitruration), de chrome (chromisation), d’aluminium (calorisation), de zinc (shérardisation), de bore (boruration) ou de silicium (siliciuration).
Appareillages et installations
La réalisation des traitements thermiques peut être considérée sous trois aspects principaux.
• La conception des fours et du matériel de traitement doit être appropriée aux produits à traiter et aux objectifs à réaliser. Pour le traitement des pièces de petites dimensions, traitées unitairement ou par petites quantités, comme les outils ou les pièces d’outillage, on utilise toujours des fours statiques, ou fours dormants, généralement à moufle réfractaire. Pour les produits longs (barres, tubes, fils, feuillards, tôles, etc.) ou pour le traitement de pièces en grandes séries, on utilise des fours continus à passage, ou fours tunnels, dont la partie chauffante peut atteindre plusieurs dizaines de mètres. Dans ces fours, le transport des produits est assuré par un tapis ou une chaîne, par des rouleaux commandés, par des plateaux qui avancent sur la sole par un système poussant ou par secousses, ou encore par la traction du produit à travers le four (fil, feuillard). Pour les pièces lourdes et de grandes dimensions (lingots, ébauches de forge), les fours pots ou les fours puits, construits dans le sol de l’atelier, permettent une manutention par des ponts roulants. Lorsqu’il s’agit d’effectuer le recuit de pièces de fonderie ou de grandes ébauches de forgeage, les fours possèdent une sole mobile horizontale ou verticale, sur laquelle est plus facilement déposée la pièce. Les fours à sole tournante, de même que les fours à cornue rotative, sont adaptés au traitement en série de pièces de moyennes ou de petites dimensions. Les fours cloches permettent le traitement de bandes, de feuillards, de fils en rouleaux ou en bobines, qui peuvent être déposés sur des embases coiffées par la cloche chauffante. Pour les alliages légers traités à température moyennement élevée, la convection forcée par brassage de l’atmosphère du four permet un chauffage plus homogène.
Les installations classiques de trempe possèdent un bac aménagé (réchauffage ou refroidissement du liquide, agitation, circulation) à l’extérieur du four. Une évolution particulièrement intéressante a été la réalisation de fours avec bac de trempe incorporé, qui permettent, à partir d’un cycle défini, le traitement totalement automatique du chauffage, de la trempe et du revenu.
• Le mode de chauffage des fours dépend de la température à atteindre, de l’atmosphère du four et des conditions économiques. Il est réalisé soit par le gaz (flamme, tubes radiants), soit par des moyens électriques (résistances, tubes, baguettes, induction à moyenne ou à haute fréquence, électrodes plongeantes dans un bain de sels). Certains fours peuvent être réglés avec une précision de maintien de la température à ± 3 °C par exemple à 1 000 °C.
• L’utilisation d’atmosphères contrôlées de protection (neutre ou légèrement réductrice ou carburante) ainsi que le traitement sous vide préviennent l’oxydation superficielle des pièces et les réactions chimiques de surface. Le traitement avec chauffage, suivi de trempe en bains de sels, particulièrement adapté aux pièces d’outillage, permet l’homogénéisation dans la répartition de la température et la protection des pièces.
R. Le R.
➙ Acier / Alliage / Aluminium / Cémentation / Cuivre / Électrométallurgie / Fer / Fonte / Four / Métallographie.